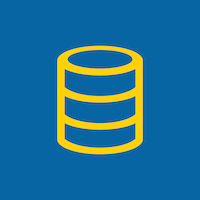
AI4I 2020 Predictive Maintenance Dataset
Donated on 8/29/2020
The AI4I 2020 Predictive Maintenance Dataset is a synthetic dataset that reflects real predictive maintenance data encountered in industry.
Dataset Characteristics
Multivariate, Time-Series
Subject Area
Computer Science
Associated Tasks
Classification, Regression, Causal-Discovery
Feature Type
Real
# Instances
10000
# Features
6
Dataset Information
Additional Information
Since real predictive maintenance datasets are generally difficult to obtain and in particular difficult to publish, we present and provide a synthetic dataset that reflects real predictive maintenance encountered in industry to the best of our knowledge.
Has Missing Values?
No
Introductory Paper
By S. Matzka. 2020
Published in International Conference on Artificial Intelligence for Industries
Variables Table
Variable Name | Role | Type | Description | Units | Missing Values |
---|---|---|---|---|---|
UID | ID | Integer | no | ||
Product ID | ID | Categorical | no | ||
Type | Feature | Categorical | no | ||
Air temperature | Feature | Continuous | K | no | |
Process temperature | Feature | Continuous | K | no | |
Rotational speed | Feature | Integer | rpm | no | |
Torque | Feature | Continuous | Nm | no | |
Tool wear | Feature | Integer | min | no | |
Machine failure | Target | Integer | no | ||
TWF | Target | Integer | no |
0 to 10 of 14
Additional Variable Information
The dataset consists of 10 000 data points stored as rows with 14 features in columns UID: unique identifier ranging from 1 to 10000 product ID: consisting of a letter L, M, or H for low (50% of all products), medium (30%) and high (20%) as product quality variants and a variant-specific serial number air temperature [K]: generated using a random walk process later normalized to a standard deviation of 2 K around 300 K process temperature [K]: generated using a random walk process normalized to a standard deviation of 1 K, added to the air temperature plus 10 K. rotational speed [rpm]: calculated from a power of 2860 W, overlaid with a normally distributed noise torque [Nm]: torque values are normally distributed around 40 Nm with a σ = 10 Nm and no negative values. tool wear [min]: The quality variants H/M/L add 5/3/2 minutes of tool wear to the used tool in the process. and a 'machine failure' label that indicates, whether the machine has failed in this particular datapoint for any of the following failure modes are true. The machine failure consists of five independent failure modes tool wear failure (TWF): the tool will be replaced of fail at a randomly selected tool wear time between 200 – 240 mins (120 times in our dataset). At this point in time, the tool is replaced 69 times, and fails 51 times (randomly assigned). heat dissipation failure (HDF): heat dissipation causes a process failure, if the difference between air- and process temperature is below 8.6 K and the tool’s rotational speed is below 1380 rpm. This is the case for 115 data points. power failure (PWF): the product of torque and rotational speed (in rad/s) equals the power required for the process. If this power is below 3500 W or above 9000 W, the process fails, which is the case 95 times in our dataset. overstrain failure (OSF): if the product of tool wear and torque exceeds 11,000 minNm for the L product variant (12,000 M, 13,000 H), the process fails due to overstrain. This is true for 98 datapoints. random failures (RNF): each process has a chance of 0,1 % to fail regardless of its process parameters. This is the case for only 5 datapoints, less than could be expected for 10,000 datapoints in our dataset. If at least one of the above failure modes is true, the process fails and the 'machine failure' label is set to 1. It is therefore not transparent to the machine learning method, which of the failure modes has caused the process to fail
Dataset Files
File | Size |
---|---|
ai4i2020.csv | 509.8 KB |
Reviews
There are no reviews for this dataset yet.
pip install ucimlrepo
from ucimlrepo import fetch_ucirepo # fetch dataset ai4i_2020_predictive_maintenance_dataset = fetch_ucirepo(id=601) # data (as pandas dataframes) X = ai4i_2020_predictive_maintenance_dataset.data.features y = ai4i_2020_predictive_maintenance_dataset.data.targets # metadata print(ai4i_2020_predictive_maintenance_dataset.metadata) # variable information print(ai4i_2020_predictive_maintenance_dataset.variables)
AI4I 2020 Predictive Maintenance Dataset [Dataset]. (2020). UCI Machine Learning Repository. https://doi.org/10.24432/C5HS5C.
DOI
License
This dataset is licensed under a Creative Commons Attribution 4.0 International (CC BY 4.0) license.
This allows for the sharing and adaptation of the datasets for any purpose, provided that the appropriate credit is given.