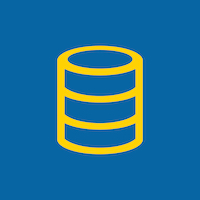
Condition Based Maintenance of Naval Propulsion Plants
Donated on 9/10/2014
Data have been generated from a sophisticated simulator of a Gas Turbines (GT), mounted on a Frigate characterized by a COmbined Diesel eLectric And Gas (CODLAG) propulsion plant type.
Dataset Characteristics
Multivariate
Subject Area
Computer Science
Associated Tasks
Regression
Feature Type
Real
# Instances
11934
# Features
-
Dataset Information
Additional Information
The experiments have been carried out by means of a numerical simulator of a naval vessel (Frigate) characterized by a Gas Turbine (GT) propulsion plant. The different blocks forming the complete simulator (Propeller, Hull, GT, Gear Box and Controller) have been developed and fine tuned over the year on several similar real propulsion plants. In view of these observations the available data are in agreement with a possible real vessel. In this release of the simulator it is also possible to take into account the performance decay over time of the GT components such as GT compressor and turbines. The propulsion system behaviour has been described with this parameters: - Ship speed (linear function of the lever position lp). - Compressor degradation coefficient kMc. - Turbine degradation coefficient kMt. so that each possible degradation state can be described by a combination of this triple (lp,kMt,kMc). The range of decay of compressor and turbine has been sampled with an uniform grid of precision 0.001 so to have a good granularity of representation. In particular for the compressor decay state discretization the kMc coefficient has been investigated in the domain [1; 0.95], and the turbine coefficient in the domain [1; 0.975]. Ship speed has been investigated sampling the range of feasible speed from 3 knots to 27 knots with a granularity of representation equal to tree knots. A series of measures (16 features) which indirectly represents of the state of the system subject to performance decay has been acquired and stored in the dataset over the parameter's space. Check the README.txt file for further details about this dataset.
Has Missing Values?
No
Variables Table
Variable Name | Role | Type | Description | Units | Missing Values |
---|---|---|---|---|---|
no | |||||
no | |||||
no | |||||
no | |||||
no | |||||
no | |||||
no | |||||
no | |||||
no | |||||
no |
0 to 10 of 16
Additional Variable Information
- A 16-feature vector containing the GT measures at steady state of the physical asset: Lever position (lp) [ ] Ship speed (v) [knots] Gas Turbine (GT) shaft torque (GTT) [kN m] GT rate of revolutions (GTn) [rpm] Gas Generator rate of revolutions (GGn) [rpm] Starboard Propeller Torque (Ts) [kN] Port Propeller Torque (Tp) [kN] Hight Pressure (HP) Turbine exit temperature (T48) [C] GT Compressor inlet air temperature (T1) [C] GT Compressor outlet air temperature (T2) [C] HP Turbine exit pressure (P48) [bar] GT Compressor inlet air pressure (P1) [bar] GT Compressor outlet air pressure (P2) [bar] GT exhaust gas pressure (Pexh) [bar] Turbine Injecton Control (TIC) [%] Fuel flow (mf) [kg/s] - GT Compressor decay state coefficient - GT Turbine decay state coefficient
Dataset Files
File | Size |
---|---|
UCI CBM Dataset/data.txt | 3.3 MB |
UCI CBM Dataset/.DS_Store | 6 KB |
UCI CBM Dataset/README.txt | 5.2 KB |
UCI CBM Dataset/Features.txt | 758 Bytes |
__MACOSX/UCI CBM Dataset/._.DS_Store | 120 Bytes |
0 to 5 of 7
Reviews
There are no reviews for this dataset yet.
pip install ucimlrepo
from ucimlrepo import fetch_ucirepo # fetch dataset condition_based_maintenance_of_naval_propulsion_plants = fetch_ucirepo(id=316) # data (as pandas dataframes) X = condition_based_maintenance_of_naval_propulsion_plants.data.features y = condition_based_maintenance_of_naval_propulsion_plants.data.targets # metadata print(condition_based_maintenance_of_naval_propulsion_plants.metadata) # variable information print(condition_based_maintenance_of_naval_propulsion_plants.variables)
Coraddu, A., Oneto, L., Ghio, A., Savio, S., Anguita, D., & Figari, M. (2014). Condition Based Maintenance of Naval Propulsion Plants [Dataset]. UCI Machine Learning Repository. https://doi.org/10.24432/C5K31K.
Creators
Andrea Coraddu
Luca Oneto
Alessandro Ghio
Stefano Savio
Davide Anguita
Massimo Figari
DOI
License
This dataset is licensed under a Creative Commons Attribution 4.0 International (CC BY 4.0) license.
This allows for the sharing and adaptation of the datasets for any purpose, provided that the appropriate credit is given.